ROD TYPE (SR)
Compact 1-axis robot (electric cylinder) rod type with excellent durability applicable to the needs of the space saving and low cost is introduced.
![]() |
SR type (Rod type) : Suitable for transfer work with the tool attached to the rod tip, alignment and positioning, and tightening work while pushing the workpiece by the rod. -Stroke:50 to 300 mm |
Features
TRANSERVO series
1. New control method combines the best features of servo and stepping motors!
Stepping motors provide great features such as low cost , yet they have a drastic drop in torque at high speeds and heavy current consumption when stopped. The TRANSERVO by YAMAHA eliminates all these problems by adopting an innovative vector control method. In effect, the TRANSERVO delivers the same functions of a servo motor while using a lower cost stepping motor.
Energy saver! Perfect stop! |
![]() |
2. Environmentally rugged resolver provides closed loop control
The resolver used for detecting the motor position is the same reliable resolver as used in our high-level robots. Resolver offer stable position detection even in harsh environments containing dust or oil, etc. Addtionally the resolution of the resolver is 20480 pulses per revolution.
The resolver is a magnetic position detector. Its structure is simple with no electronic component and no optical elements. One great feature compared to ordinary optical encoders is that there are very few points where a failure might occur. Vast quantities of resolvers are used in fields like aviation and the automobile industry where reliability is essential and also because they are highly tough in harsh environments with a low failure rate.
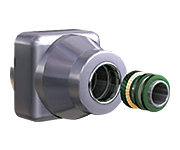
Rod type
1. Long-Term Maintenance Free
A lubricator used in the ball screw and a contact scraper provides long-life and maintenance-free operation. maintenance free operation.
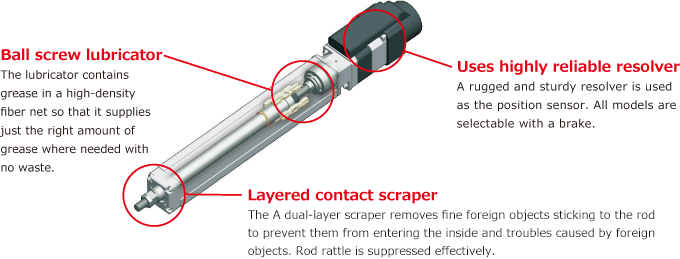
2. Needs no maintenance for long periods
Grease lubrication on the ball screw is usually lost a little bit at a time with ball screw movement. The SR type has a lubricator that supplies grease lost over long periods to ensure near maintenance-free operation Note.
Note. The maintenance-free period is within the running life of the robot.
3. Grease-saving lubrication system
The lubricator uses a high-density fiber net that supplies just the right amount of grease in an eco-friendly lubrication system that wastes no grease.
4. Prevents contaminant particles
The dual-layer scraper in contact with the rod removes micro contaminant particles with near-perfect performance. It scrapes away tiny par ticles adhering to the rod in a multi-step operation that prevent trouble from contaminants that might otherwise penetrate to internal parts. Synthetic foam rubber with a selflubricating function ensures low-friction resistance.
5. Grease gun nozzle tube (YAMAHA recommended nozzle tube)
This nozzle tube is even usable when there is little space around the grease port. For example, when the SR04 or SR05 space-saving model is used with the motor facing up, the grease port is positioned on the side of the robot body. This may make it difficult to refill grease depending on the positions of other robots or peripheral units.
Model : KCU-M3861-00
Note. This nozzle tube can be attached to a commercially available ordinary grease gun.
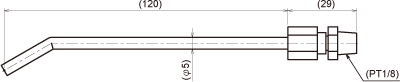
Type | Model | Size (mm) | Lead (mm) | Maximum payload (kg) | Maximum speed (mm/sec) | Stroke (mm) | |
Horizontal | Vertical | ||||||
Standard | W48xH56.5 | 12 | 10 | 4 | 500 | 50 to 200 | |
6 | 20 | 8 | 250 | ||||
W48xH58 | 12 | 25 | 5 | 500 | 50 to 300 | ||
6 | 40 | 12 | 250 | ||||
2 | 45 | 25 | 80 | ||||
SR05-SSR05-R(L)(494 KB) | W56.4xH71 | 12 | 50 | 10 | 300 | 50 to 300 | |
6 | 55 | 20 | 150 | ||||
2 | 60 | 30 | 50 | ||||
With support guide | SRD03-SSRD03-U(352 KB) | W105xH56.5 | 12 | 10 | 3.5 | 500 | 50 to 200 |
6 | 20 | 7.5 | 250 | ||||
SRD04-SSRD04-U(359 KB) | W135xH58 | 12 | 25 | 4 | 250 | 50 to 300 | |
6 | 40 | 11 | 250 | ||||
2 | 45 | 24 | 80 | ||||
SRD05-SSRD05-U(365 KB) | W151xH71 | 12 | 50 | 8.5 | 300 | 50 to 300 | |
6 | 55 | 18.5 | 150 | ||||
2 | 60 | 28.5 | 50 |
Note1. Size is the approximate cross sectional size.
Note2. Maximum speed varies with the payload. See the SR type page for more details.
Note3. Maximum speed decreases due to ball screw critical speed when the stroke is long.
Maximum operating speed may drop when an external force is applied or the support guide sliding resistance is large.