BELT TYPE (BD)
Three types that are newly added to the TRANSERVO series, slider table type, rotary type, and belt type, are introduced.
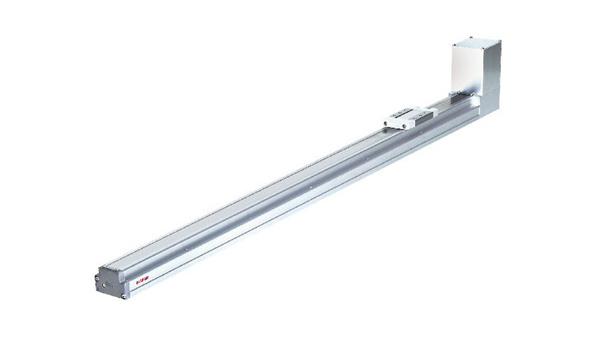
Belt type (BD) : Universality, energy-saving and low impact achieved with multi-position positioning unique to motorized devices. The compact size supports a maximum 2000 strokes.
Features
TRANSERVO series
1. New control method combines the best features of servo and stepping motors!
Stepping motors provide great features such as low cost , yet they have a drastic drop in torque at high speeds and heavy current consumption when stopped. The TRANSERVO by YAMAHA eliminates all these problems by adopting an innovative vector control method. In effect, the TRANSERVO delivers the same functions of a servo motor while using a lower cost stepping motor.
Energy saver! Perfect stop! |
![]() |
2. Environmentally rugged resolver provides closed loop control
The resolver used for detecting the motor position is the same reliable resolver as used in our high-level robots. Resolver offer stable position detection even in harsh environments containing dust or oil, etc. Addtionally the resolution of the resolver is 20480 pulses per revolution.
The resolver is a magnetic position detector. Its structure is simple with no electronic component and no optical elements. One great feature compared to ordinary optical encoders is that there are very few points where a failure might occur. Vast quantities of resolvers are used in fields like aviation and the automobile industry where reliability is essential and also because they are highly tough in harsh environments with a low failure rate.
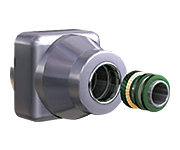
Features
Belt type
1. Belt type applicable to long stroke
-Applicable to up to 2000 mm-stroke.
-High speed movement at a speed of up to 1500 mm/sec. can be made.
-Maximum payload 14 kg
-Main body can be installed without disassembling the robot.
-Shutter is provided as standard equipment. This prevents grease scattering or entry of foreign object.
Type | BD04 (334 KB) | BD05 (344 KB) | BD07 (342 KB) | |
Motor | 28□Step motor | 42□Step motor | 56□Step motor | |
Resolution | 4096 | 20480 | 20480 | |
Repeated positioning accuracy (mm) *1 | +/-0.1 | +/-0.1 | +/-0.1 | |
Drive method | belt | belt | belt | |
Equivalent lead (mm) | 48 | 48 | 48 | |
Maximum speed (mm/sec)*2 | 1100 | 1400 | 1500 | |
Maximum payload (kg) | 1 | 5 | 14 | |
Stroke (mm) | 300,500,600,700, 800,900,1000 |
300,500,600,700,800,900, 1000,1200,1500,1800,2000 |
300,500,600,700,800,900, 1000,1200,1500,1800,2000 |
|
Static loading moment (N・m) |
MY | 10 | 27 | 46 |
MP | 10 | 27 | 46 | |
MR | 20 | 52 | 101 | |
Allowable overhang | ||||
Overall length(mm) | Stroke+195.5 | Stroke+241.8 | Stroke+285.6 | |
Maximum outside dimension of body cross-section (mm) | W40+H101.9 | W58+H123 | W70+H147.5 | |
Cable length (m) | Standard:1 / Option:3,5,10 |
*1. Positioning repeatability in one direction.
*2. The speed may vary depending on the payload. Check the speed vs. payload graph (reference).