LOW COST HIGH PERFORMANCE SCARA robots
For improved efficiency and reliability in production at affordable price
|
LOW COST HIGH PERFORMANCE SCARA ROBOT YK-XE
Efficiency In Production For improved efficiency and reliability in production at affordable price -Arm length:400mm to 710mm |
Features
1. Optimal for transfer and assembly of automotive parts

2. Improvement of productivity by high-speed operation
By reviewing the arm structure, the vibration is reduced and the motion is optimized to shorten the standard cycle time.
High-speed, less-vibration, and agile operation contributes to improvement of the productivity.
|
3. For a wide variety of applications Maximum payload 4kg to 10kg
The models support a wide variety of fields such as assembly work that requires a high precision or food sorting work that requires a high-speed operation. As the maximum payload is 10 kg, heavy workpieces such as automotive parts can also be supported.
4. Application Examples
![]() |
![]() |
![]() |
![]() |
Palletizing | Loading and unloading | Assembly (or Pick & Place) | Inspection |
5. Affordable Price and Improved Performance
Both the high operation performance and affordable price are achieved. Production equipment with high cost performance can be constructed.
![]() |
![]() |
![]() |
![]() |
6. Improved User Interface
Enhanced size and numbers of air tubes and user I/O for end effectors. Tubes and wires are positioned for easy layout and reduced risk of disconnection. (YK610XE-10 and YK710XE-10)
![]() |
![]() |
* YK400XE-4 provides the user wiring x 10 cores and the User tubing φ4 x 3 pcs.
7. In Yamaha YK-XE series Acceleration/Deceleration is optimized automatically
The optimal acceleration and deceleration are automatically selected from the arm posture at the time of operation start and the arm posture at the time of operation end. The motor peak torque or the tolerable peak torque of the speed reducer is not exceeded by inputting only three parameters*. The full power of the motor is always output to maintain the high acceleration/deceleration.
* Payload, R-axis moment of inertia, and offset amount of R-axis moment of inertia
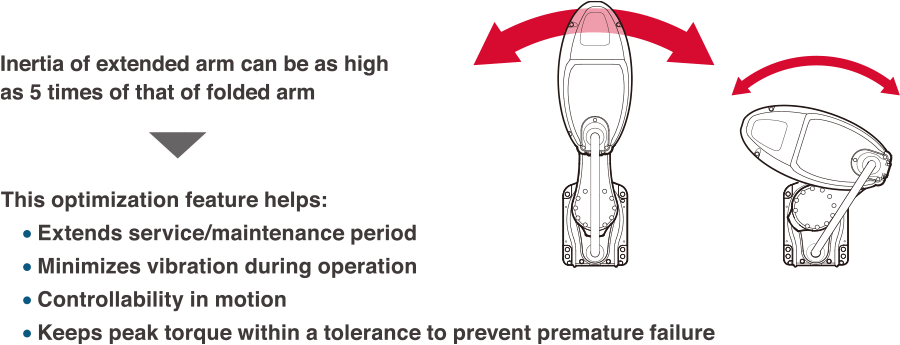
8. Through-shaft and through-cap have been added.
“Through-shaft” or “through-cap” option for wiring and tubing that is convenient to run the air tubing and wiring can be selected. The wiring and tubing routes can be investigated easily without designing and manufacturing a stay for installing the wiring and tubing. In addition, by passing the wiring and tubing through the inside of the main body, worries about wire breakage or disconnection are reduced during operation. (Only through-shaft is available in YK400XE-4.) |
![]() |
9. Brake release switch is selectable.
In the emergency stop state, the Z-axis brake is released and the Z-axis can be moved up or down while the brake release switch is held down. Releasing the switch applies the brake to the Z-axis. This improves the convenience during installation adjustment. |
![]() |
10. Drop-In upgrade by common platform design
The installation position of the YK400XE-4 is fully compatible with that of the conventional model YK400XR. This ensures easy replacement work.
![]() |
![]() |
11. Easier operation in combination with the RCX340 controller
RCX340 comprehensive controller brings out maximum potential of YK400XE robot system. Optional integrated vision system “iVY2” provides simplified image processing. Choice of PC Programming Software or Teaching Pendant available.
![]() |
![]() |
![]() |
12. Simple and Easy integration of Vision System
Robot controller with vision and gripper interface
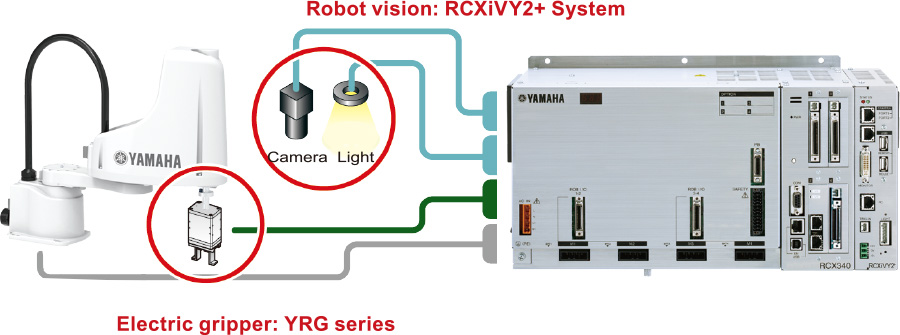
13. Compatible with various field networks
The robot is compatible with full field networks such as CC-Link, EtherNet/IP™, DeviceNet™, PROFIBUS, PROFINET, and EtherCAT.

14. Reliability backed by 43-year experience of SCARA robot development
Originally developed in-house to provide durable and accurate motion control in harsh environment of motorcycle manufacturing, Yamaha SCARA robot has been “road tested” and proven over 43 years in various fields.
*The product release was 1984.
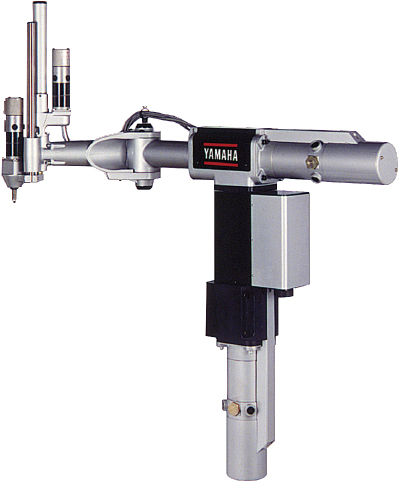
Specifications
YK400XE-4 (771 KB) | X-axis | Y-axis | Z-axis | R-axis | ||
Axis specifi cations | Arm length(mm) | 225 | 175 | 150 | - | |
Rotation angle(°) | ±132 | ±150 | - | ±360 | ||
AC servo motor output(W) | 200 | 100 | 100 | 100 | ||
Deceleration mechanism |
Transmission method |
Motor to speed reducer | Direct-coupled | Timing belt | ||
Speed reducer to output | Direct-coupled | Timing belt | ||||
Repeatability* (XYZ:mm)(R:°) | ±0.01 | ±0.01 | ±0.01 | |||
Maximum speed (XYZ:m/sec)(R:°/sec) | 6 | 1.1 | 2600 | |||
Maximum payload (kg) | 4 kg (Standard specifi cation), 3 kg (Option specifi cations****) | |||||
Standard cycle time: with 2kg payload** (sec) | 0.41 | |||||
R-axis tolerable moment of inertia*** (kg*sq.m) | 0.05 (0.5 kgfcms^2) | |||||
User wiring(sq×wires) | 0.2 × 10 | |||||
User tubing (Outer diameter) | φ4×3 | |||||
Travel limit | 1.Soft limit 2.Mechanical stopper (X,Y,Z axis) | |||||
Robot cable length(m) | Standard: 3.5 m Option: 5 m, 10 m | |||||
Weight(kg) | 17 |
*This is the value at a constant ambient temperature. (X,Y axes)
**When reciprocating 300mm in horizontal and 25mm in vertical directions and performing the coarse positioning arch operation.
***The acceleration coefficient is set automatically in accordance with the tip weight and offset amount for R-axis moment of inertia settings.
****Maximum payload of option specifications (with user wiring/tubing through spline type) is 3kg.
YK510XE-10 (790 KB) | X-axis | Y-axis | Z-axis | R-axis | ||
Axis specifi cations | Arm length(mm) | 235 | 275 | 200 | - | |
Rotation angle(°) | ±134 | ±152 | - | ±360 | ||
AC servo motor output(W) | 400 | 200 | 200 | 200 | ||
Deceleration mechanism |
Transmission method |
Motor to speed reducer | Direct-coupled | Timing belt | ||
Speed reducer to output | Direct-coupled | Timing belt | ||||
Repeatability* (XYZ:mm)(R:°) | ±0.01 | ±0.01 | ±0.01 | |||
Maximum speed (XYZ:m/sec)(R:°/sec) | 7.8 | 2 | 2600 | |||
Maximum payload (kg) | 10 kg (Standard specifi cation), 9 kg (Option specifi cations****) | |||||
Standard cycle time: with 2kg payload** (sec) | 0.38 | |||||
R-axis tolerable moment of inertia*** (kg*sq.m) | 0.3 | |||||
User wiring(sq×wires) | 0.2 × 10 | |||||
User tubing (Outer diameter) | φ6×3 | |||||
Travel limit | 1.Soft limit 2.Mechanical stopper (X,Y,Z axis) | |||||
Robot cable length(m) | Standard: 3.5 m Option: 5 m, 10 m | |||||
Weight(kg) | 25 |
*This is the value at a constant ambient temperature. (X,Y axes)
**When reciprocating 300mm in horizontal and 25mm in vertical directions and performing the coarse positioning arch operation.
***The acceleration coefficient is set automatically in accordance with the tip weight and offset amount for R-axis moment of inertia settings.
****Maximum payload of option specifications (with user wiring/tubing through spline type) is 3kg.
YK610XE-10 (675 KB) | X-axis | Y-axis | Z-axis | R-axis | ||
Axis specifi cations | Arm length(mm) | 335 | 275 | 200 | - | |
Rotation angle(°) | ±134 | ±152 | - | ±360 | ||
AC servo motor output(W) | 400 | 200 | 200 | 200 | ||
Deceleration mechanism |
Transmission method |
Motor to speed reducer | Direct-coupled | Timing belt | ||
Speed reducer to output | Direct-coupled | Timing belt | ||||
Repeatability* (XYZ:mm)(R:°) | ±0.01 | ±0.01 | ±0.01 | |||
Maximum speed (XYZ:m/sec)(R:°/sec) | 8.6 | 2 | 2600 | |||
Maximum payload (kg) | 10 kg (Standard specifi cation), 9 kg (Option specifi cations****) | |||||
Standard cycle time: with 2kg payload** (sec) | 0.39 | |||||
R-axis tolerable moment of inertia*** (kg*sq.m) | 0.3 | |||||
User wiring(sq×wires) | 0.2 × 20 | |||||
User tubing (Outer diameter) | φ6×3 | |||||
Travel limit | 1.Soft limit 2.Mechanical stopper (X,Y,Z axis) | |||||
Robot cable length(m) | Standard: 3.5 m Option: 5 m, 10 m | |||||
Weight(kg) | 25 |
*This is the value at a constant ambient temperature. (X,Y axes)
**When reciprocating 300mm in horizontal and 25mm in vertical directions and performing the coarse positioning arch operation.
***The acceleration coefficient is set automatically in accordance with the tip weight and offset amount for R-axis moment of inertia settings.
****Maximum payload of option specifications (with user wiring/tubing through spline type) is 3kg.
YK710XE-10 (667 KB) | X-axis | Y-axis | Z-axis | R-axis | ||
Axis specifi cations | Arm length(mm) | 435 | 275 | 200 | - | |
Rotation angle(°) | ±134 | ±152 | - | ±360 | ||
AC servo motor output(W) | 400 | 200 | 200 | 200 | ||
Deceleration mechanism |
Transmission method |
Motor to speed reducer | Direct-coupled | Timing belt | ||
Speed reducer to output | Direct-coupled | Timing belt | ||||
Repeatability* (XYZ:mm)(R:°) | ±0.02 | ±0.01 | ±0.01 | |||
Maximum speed (XYZ:m/sec)(R:°/sec) | 9.5 | 2 | 2600 | |||
Maximum payload (kg) | 10 kg (Standard specifi cation), 9 kg (Option specifi cations****) | |||||
Standard cycle time: with 2kg payload** (sec) | 0.42 | |||||
R-axis tolerable moment of inertia*** (kg*sq.m) | 0.3 | |||||
User wiring(sq×wires) | 0.2 × 20 | |||||
User tubing (Outer diameter) | φ6×3 | |||||
Travel limit | 1.Soft limit 2.Mechanical stopper (X,Y,Z axis) | |||||
Robot cable length(m) | Standard: 3.5 m Option: 5 m, 10 m | |||||
Weight(kg) | 26 |
*This is the value at a constant ambient temperature. (X,Y axes)
**When reciprocating 300mm in horizontal and 25mm in vertical directions and performing the coarse positioning arch operation.
***The acceleration coefficient is set automatically in accordance with the tip weight and offset amount for R-axis moment of inertia settings.
****Maximum payload of option specifications (with user wiring/tubing through spline type) is 3kg.
Catalog